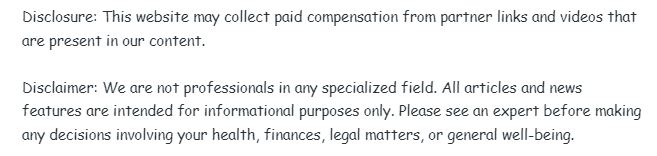

As anyone in the construction industry knows, safety is the top priority for those working in construction. The reasons behind this concern for safety, however, go beyond what some may think of as obvious. Of course, the main reason is that nobody wants a person to get injured on the job. This is the worst case scenario for any employer, especially when the injured person in question is working with a crane, which is typically a piece of equipment associated with a host of different problems. If a person is hurt on the job while working on a crane, their employers can often be held responsible, leading to a number of different legal and financial problems. If the person owning the crane used is not the employer, they too can be potentially held responsible on some level. Even when people are not physically hurt while working on a crane, the potential for danger remains. The crane, too, can be damaged if improperly cared for or handled. A damaged crane can cost a large amount of money to repair, and of course, an even larger amount of money to replace. The use of outrigger crane pads, along with other products and devices, can lower the risk of damage to cranes and physical injury to workers. Let’s look into crane pads — why we use them, and what they’re made of.
Outrigger Crane Pads: What They’re Made Of
One of the most important things to be aware of when buying crane pads is the material of which the crane pads you’re buying are made. Different materials clearly suit different purposes, and yield a variety of results. One type of crane pad is made from a thermoplastic material. This engineered material is seven times lighter than steel and four times lighter than aluminum, making it easier to transport and manipulate. Of course, there are plenty of purposes which this light material would be perfect. But it’s not the only material from which crane pads are made. Steel crane pads are also on the market. While these pads may be more difficult to move and manipulate, they’re also tougher. Therefore, if you’re working in a setting that is rougher or requires a large amount of tress to be put on the crane pads, steel crane pads may be a better option to look into.
Buying Crane Pads: What To Keep In Mind
There are a variety of factors to consider when buying crane pads, even if you’ve already decided upon the material you want. When buying an outrigger pad, you should focus on these three top factors: ground conditions, the size of the outrigger food, and outrigger ground conditions. The last thing that anyone wants to do is buy an outrigger pad, only to find that it’s useless in the specific conditions in which you’re working. Buying the wrong outrigger pads could also pose a potential danger not only to the crane itself, but the people operating the crane.
Crane Pads In Use: Operating Crane With Outrigger Pads
After you’ve bought the outrigger pads you need, there are several things to be aware of when actually operating a crane. OSHA has many requirements that crane operators must adhere to. The ground on which a crane is assembled must be firm, drained, and graded sufficiently. This is done in conjunction with supportive materials including blocking, cribbing, pads, and mats to provide adequate support and levelness. The operating conditions are also dependent on the type of crane being operated. A mobile crane is much more likely to tip than an immobile, grounded crane — for obvious reasons. The chances of a mobile crane tipping are heightened if the load the crane is carrying is too heavy. This is, unfortunately, all too common. The CDC reports that the rate of crane upsets is about one for every 10,000 hours of use. Therefore, it’s clearly necessary that these cranes be grounded in every way possible.