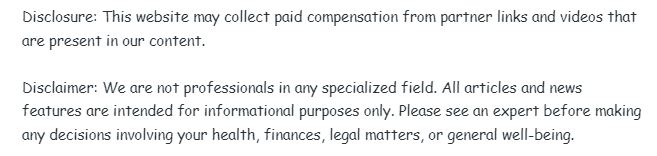

Welding has a long history and is one of the most important industrial processes in manufacturing today. That’s why there is a constant demand for qualified and experienced workers in this field. As well as some formal training, on the job experience counts for a lot when it comes to hiring. Training helps workers to keep up their skills to the latest industry standards. A current knowledge of all techniques and parts like weld on hinges and purge equipment is necessary to keep your knowledge current and relevant.
Welding is a major part of manufacturing
Welding is one of the mainstays of industrial manufacturing in the U.S. and around the world. Archeologists have discovered evidence of welding from as far back as 3,500 B.C. Today, two thirds of all welding jobs are concentrated in the manufacturing industries. Welders are part of the fabrication process and manufacture products by joining parts made of materials like steel, brass, stainless steel and aluminum.
More than half of all products made in the U.S. need welding. That’s why there is a constant demand for workers in this field. At the present time, there are around half a million welders employed across the country. Industries that hire welders include construction, steel, aerospace, and motor vehicles. Welding methods like arc welding, soldering, brazing, casting and bronzing can be learned in school or acquired on the job.
A career in welding
According to the Bureau of Labor Statistics, the demand for qualified workers will continue to grow at the rate of 4% between 2014 and 2024. The hourly rate earned by welders is $19.70. Anyone considering this career should have both physical strength and the skills to handle heavy and potentially hazardous machinery and materials. Problem solving skills and communication are also relevant to this field.
The minimum qualification for a welding job is a high school diploma or the equivalent. A technical education will add knowledge of handling equipment like weld on hinges, non sparking tools, pipe alignment clamps and purge monitors. Many employers prefer to hire workers who already possess technical skills in welding, whether through formal training or on the job experience.
Staying current with with latest techniques
As well as basic training, a willingness to continue to learn is essential for the profession. Techniques and technology change very quickly, and businesses are at a disadvantage when they cannot adapt. It is estimated that manufacturers lose thousands of dollars when they use outdated processes to align pipes and fittings.
Workers who are familiar with the latest technology and methods for parts and processes like weld on hinges and non sparking tools for welding will be at an advantage. A willingness to relocate and to move where the jobs are will also be an advantage in this field.
Welding is an essential part of industrial production today and welders will continue to be in demand for the foreseeable future. As well as basic training, workers should have on the job experience and a willingness to continue to learn the latest technology. Equipment like purge monitors and weld on hinges is constantly being changed and modified with the latest technology, and workers who can stay up to date will have an advantage.