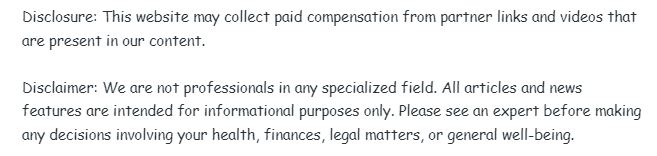
The air compressor system is a very important tool, so important that it is used in just under one third of all manufacturing facilities seen throughout the United States. After all, compressed air systems are able to be used for a wide variety of applications, making them universally useful and important in many aspects of our broad manufacturing world. For one thing, compressed air systems for auto repair have become essential in the automotive industry. After all, most of us need to drive on a day to day basis, from going to work or school to picking up our kids to even performing daily tasks such as getting groceries or going to the doctor.
Of course, compressed air systems are not just used for various automotive purposes. In addition to compresses air systems for auto repair uses, compressed air systems for heavy equipment usage is also considered an important applications for these compressed air systems. Again, various types of heavy machinery are quite regularly used all throughout the country and therefore, it is important that we have the tools needed to service this heavy machinery, which comes in many different shapes and sizes and can be used to accomplish many a goal.
Even past these uses, there are still more. Compressed air systems for wood working purposes are also commonly seen – and considered to be quite highly important as well. After all, wood working is a common thing here in the United States, as wood still has a great many uses both in our day to day life as well as in many structural aspects of our lives as well (such as in our homes, to name just one example out of many). Ultimately, this means that having the right tools, like compressed air piping systems, ready to go for wood working purposes is something of an absolute must, to say the very least.
So with all these applications for compressed air systems, it is clear that these systems will need to be well taken care of, from their air compressor piping to their air fittings and beyond. This regular maintenance will likely end up being essential for the function of the systems as a whole – and for the desired end result for whatever product it is that is being worked on. Air compressor piping plays a big part of this. If air compressor piping is damaged in any way, it is far too likely that issues with the whole air compressor system in its entirety will develop. For instance, even an air compressor piping leak that is a mere one eighth of an inch in diameter can lead to a loss of up to $12,000 over the course of a single year in a system that has 100 psi. In some air compressor systems, a minor leak in the air compressor piping can prove to be even more damaging indeed. Therefore, regular maintenance to check up on any given air compressor system and set of air compressor piping is quite essential, as such air compressor piping can then be fixed before the problem becomes much more pronounced. When an air compressor piping issues can be rectified shortly after the issue has first developed, a great deal of problems are likely to be avoided, saving time, money, and critical resources.
Of course, energy efficiency is becoming more and more of a priority in the use of various air compressor systems and even air compressor piping itself. For one thing, converting the heat that is developed through such systems is ideal, as up to 90% of the electrical energy that is used in any given air compressor system will be converted to heat during the process of use. Fortunately, we have found ways to harness this heat and now at least half of it can be used to heat the building or water supply, which then saves energy from needing to be generated strictly for those purposes. Not only is this hugely cost effective, but it’s very much environmentally friendly as well, which is not something that can be taken for granted by any means, as many of us know or are becoming all the more clear of with time.