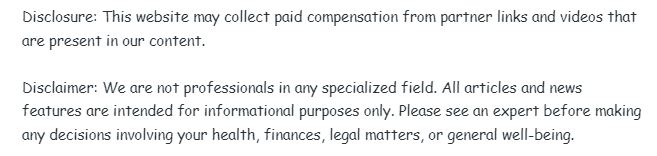

To keep the air in your house circulating in the right manner, your air compressor parts should be well maintained. Even the most reliable air compressor breaks down. The point is, do you have access to the air compressor maintenance and repair services of your master power compressor?
Consider keeping the air compressor pipes in a clean and proper working state to reduce mold in your home and eliminate pollen throughout the year. Is it possible to get a portable air pressure tank? Where can you get portable air compressor deals? There might be a friend, family member, or workmate who has dealt with air compressors installation or repair services. It is advisable to seek advice from such persons to get first-hand information on the kind of services received.
On the other hand, the internet has made it easier for you to enjoy portable air compressor deals. It is as easy as searching online to find out where and when to get the discounts. It is also possible to determine a legit and reputable company by checking the feedback clients give. Get the right air compressor parts, good quality of air is vital to your health.
Looking to renovate your home? It’s smart to start with the basics. While a new tree can help your air and a sewer repair job can pinpoint potential problems before they start, the best way to get the most bang for your buck is to get to the deepest root issue. Air compressor pipes are a necessity to keep the air in your home circulating in a healthy fashion, reducing mold and eliminating pollen all days of the year. Poorly maintained air compressor pipes, on the other hand, can lead to a host of issues down the road — that’s nothing to say of what it could do to your wallet!

What Are Air Compressor Pipes?
If you want to get started on a cleaner home, you need to know about air compressor pipes and how they work. These are used in a variety of different technologies, transferring air and circulating it regularly. Studies have estimated around 70% of all manufacturers having some sort of compressed air system — likewise, any leaks or electrical issues can be highly costly and cause serious financial ramifications down the road. For example, a 1/8 inch diameter hole in a 100 PSI system can cost a whopping $1,200 per year in wasted energy, so there’s no reason to put off a maintenance job longer than necessary!
How Often Are They Used?
It’s actually harder to find what they aren’t used for. Air compressor pipes are a staple of many a building, residential or institution, and are used on a daily basis. Around 80% to 90% of the electrical energy used by an air compressor system is converted to heat, with a properly designed heat recovery unit able to recover a whopping 90% of this heat by heating up either air or water.
What Are They Used For?
From air conditioning units to thermal tanks, air compressor pipes are used in a wide variety of appliances. Energy audits conducted by the U.S. Department of Energy (shortened to DOE) suggest that nearly 50% of all compressed air systems in either small or medium sized industrial facilities have significant low-cost energy conservation possibilities. This is fantastic news for customers and businesses alike, as clean and sustainable energy has been proven to be incredibly safe for the environment at large. That’s nothing to say of the money you’ll save, either!
What Should I Be Mindful Of?
It’s important to be aware of the little things that can go wrong. Even a minor electrical failure or leak can cost you hundreds of extra dollars on top of a poor performance. If your compressed air system doesn’t have an air receiver tank, you can add one to buffer the short-term demand changes alongside reducing the compressor’s natural cycling process. The tank is sized only to the power of the compressor at hand — for example, a 50 HP air compressor will need a 50-gallon air receiver tank to match.
Where Do I Get Started?
Eager to save money without sacrificing performance? Then it’s time to get familiar with air fitting processes, cushion clamps and air compressors. Pressure loss in a properly designed system should always be less than 10% than the compressor’s discharge pressure — you can find this information on the outlet of the compressor. If the pressure loss is greater than 10%? It’s time to evaluate your distributor system and identity any and all areas causing excessive pressure drops. Artificial demand ends up created when end use is supplying air pressure at the higher rate required. In other words, more energy for the same amount of money! While this can seem like a bit much at first, a little knowledge goes a long way.